Tác giả: Tiến sĩ Dược sĩ Nguyễn Phúc Nghĩa.
Bài viết Xay Nghiền – Rây trích trong chương 1 sách Một số quá trình và thiết bị trong công nghệ dược phẩm – giáo trình đào tạo dược sĩ đại học bộ môn Công Nghiệp Dược trường Đại học Dược Hà Nội.
Mục tiêu học tập
- Trình bày được vai trò của quá trình xay – nghiền và phân đoạn kích thước tiểu phân trong sản xuất thuốc.
- Trình bày được lý thuyết quá trình xay, nghiền.
- Trình bày được các thiết bị xay, nghiền ứng dụng trong công nghiệp dược phẩm.
- Trình bày được các kỹ thuật và thiết bị rây.
1. Xay-nghiền
Xay, nghiền là quá trình cơ bản trong sản xuất, phần lớn các vật liệu đều trải qua quá trình này ở một giai đoạn nào đó.
Xay, nghiền được định nghĩa là quá trình tác động lực cơ học vào khối chất rắn để làm giảm kích thước tiểu phân. Các tiểu phân chất rắn chịu sự biến dạng khác nhau tùy thuộc vào độ lớn của lực tác động:
- Khi lực tác động nhỏ, chất rắn sẽ bị biến dạng đàn hồi.
- Khi tăng lực tác động chất rắn sẽ bị biến dạng dẻo.
- Khi lực tăng tiếp đến một giới hạn nào đó thì chất rắn sẽ bị biến dạng gẫy vỡ.
Quá trình xay, nghiền giúp một tiểu phân tạo ra nhiều tiều phân khác có kích thước nhỏ hơn và do đó làm tăng tổng diện tích bề mặt. Xay, nghiền tạo điều kiện cho một số quá trình khác như:
- Tăng tốc độ hòa tan, đặc biệt đối với các vật liệu có độ tan kém, nhờ tăng khả năng tiếp xúc giữa tiểu phân và dịch hòa tan.
- Giảm thời gian chiết, cho phép quá trình chiết diễn ra nhanh và triệt để hơn.
- Giảm thời gian sấy vật liệu.
- Tạo thuận lợi cho quá trình trộn.
- Ngoài ra, một số nguyên liệu (như tá dược màu, tá dược trơn) cần nghiền đến kích thước mịn để phát huy tác dụng.
1.1. Lý thuyết quá trình xay, nghiền
Khi tiểu phân chịu tác động của một lực ngẫu nhiên, nó bị phân tách thành các mảnh lớn và mảnh nhỏ. Tiếp tục tăng cường độ của lực tác động, các mảnh lớn sẽ bị phân tách thành nhiều mảnh nhỏ, trong khi đó các mảnh nhỏ nhiều lên về số lượng nhưng hầu như không giảm kích thước. Đó là do kích thước các tiểu phân nhỏ phụ thuộc nhiều vào cấu trúc, còn kích thước các tiểu phân lớn phụ thuộc vào cách xay, nghiền.
Quá trình làm nhỏ tiểu phân bắt đầu từ các vết rạn và vết nứt. Vết rạn là các cấu trúc yếu, hình thành sau tác động của bất kỳ lực cơ học nào lên tiêu phân. Các vết rạn, khi chịu một lực đủ mạnh, sẽ phát triển lên thành các vết nứt. Công có ích trong quá trình nghiền tỉ lệ với độ dài của các vết nứt mới tạo ra. Các vết nứt này lan truyền nhanh qua vùng vật liệu chứa nhiều vết rạn, lớn dần và phá vỡ tiểu phân. Vật liệu có cấu trúc tinh thể sẽ bị chẻ vỡ dọc theo mặt phẳng tinh thể. Vật liệu vô định hình sẽ vỡ ngẫu nhiên. Năng lượng để làm giảm kích thước tiểu phân ngoài việc tạo ra các bề mặt mới còn để tạo ra các vết nứt và vết rạn.
Năng lượng cần cho quá trình xay, nghiền
Trong quá trình xay, nghiền, năng lượng để làm giảm kích thước tiểu phân chỉ chiếm khoảng 2%, phần năng lượng còn lại bị mất mát do làm tiểu phân biến dạng đàn hồi, làm vật liệu chuyển động trong buồng xay, nghiền, tạo ma sát giữa các tiểu phân, giữa tiểu phân với máy, sinh nhiệt, độ rung, tiếng ồn và hư hao do truyền chuyển động của mô tơ. Quan hệ giữa năng lượng sử dụng và mức độ giảm kích thước tiểu phân được thể hiện trong một số phương trình lý thuyết của Kick, Rittinger và Bond.
Lý thuyết Kick cho rằng, năng lượng E cần thiết để phá vỡ tiểu phân có liên quan trực tiếp đến tỉ lệ giảm kích thước (di/dn); trong đó: di và dn lần lượt là kích thước tiểu phân trước và sau khi nghiền. Điều đó có nghĩa là năng lượng cần thiết để làm giảm kích thước tiểu phân từ 1000 µm xuống 500 µm bằng với năng lượng cần thiết để tiểu phân giảm từ 500 µm xuống 250 µm. Phương trình được mô tả như sau:
E=Kk log(di/dn)
Kk: hằng số Kick.
Rittinger lại cho rằng năng lượng cần thiết để làm giảm kích thước tiểu phân tỉ lệ với diện tích bề mặt sinh ra:
E= Kr (Sn – Si)
Sn , Si lần lượt là diện tích bề mặt ban đầu và sau khi nghiền, Kr là hằng số Rittinger.
Phương trình Rittinger thường áp dụng cho quá trình nghiền mịn vật liệu giòn, trong đó các tiểu phân rất ít bị biến dạng và các bề mặt mới nhanh chóng được tạo ra.
Lý thuyết của Bond cho rằng, năng lượng sử dụng tỉ lệ với chiều dài vết nứt sinh ra, thường liên quan đến sự thay đổi kích thước tiểu phân theo phương trình sau:
E = 2Kb(1/(dn) – 1/(di))
Kb: hằng số Bond
di: kích thước tiểu phân lúc ban đầu,
dn: kích thước tiểu phân sau khi nghiền.
Một lý thuyết chung đại diện cho cả ba phương trình của Bond, Kick và Rittinger được Walker tập hợp lại, thể hiện mối quan hệ năng lượng (∂E) – kích thước tiểu phân (∂d) như sau:
∂E = –KW(∂d/dn)
Trong đó: KW là hằng số Walker, n là hệ số mũ.
Nếu n = 1, phương trình quay trở về phương trình Kick; n = 2 là phương trình Rittinger và n = 1,5 là phương trình Bond.
Tùy theo kích thước ban đầu của tiểu phân đem nghiền, người ta sẽ sử dụng phương trình Kick, Rittinger hoặc Bond để tính toán năng lượng tiêu thụ. Ví dụ với những tiểu phân có kích thước lớn hơn 1 pm, n = 1 và áp dụng phương trình Kick. Với những tiểu phân có kích thước nhỏ hơn 1µm, n = 2 tương ứng với phương trình Rittinger. Nếu cả hai phương trình trên đều không thể áp dụng, khi đó sử dụng n= 1,5.
Một số quan điểm cho rằng, giá trị n không hằng định mà phụ thuộc vào kích thước tiểu phân: n = f(d) Khi tiểu phân có kích thước lớn, f(d) có giá trị 1 và khi tiểu phân nhỏ đi, f(d) tăng dần đến 2.
1.2. Các yếu tố ảnh hưởng đến quá trình xay, nghiền
Hiệu suất của quá trình nghiền phụ thuộc vào bản chất và biên độ lực. Các lực tác động để làm vỡ tiểu phân gồm lực cắt, lực va đập, lực ma sát và áp suất. Trong đó, lực tác động càng lớn càng dễ làm vỡ tiểu phân.
Tốc độ tác động lực ảnh hưởng đến quá trình nghiền do có thời gian trễ giữa lực tác động và sự vỡ tiểu phân. Thông thường, nếu tác động lực nhanh, tiểu phân sẽ đáp ứng kiểu giòn và ngược lại, nếu tác động chậm, tiểu phân sẽ đáp ứng kiểu đàn hồi. Lực tác động càng nhanh, tiểu phân tạo ra càng mịn nhưng hiệu suất năng lượng được sử dụng sẽ ít đi. Để tạo ra bề mặt mới trong 1 ms sẽ cần nhiều năng lượng gấp 3 – 4 lần tạo bề mặt mới trong 1 s.
Cách cấp nguyên liệu cũng ảnh hưởng tới quá trình xay, nghiền. Nếu tốc độ cấp liệu chậm, quá trình xả nguyên liệu gần như tức thời, số lượng các hạt mịn sinh ra là ít nhất. Ngược lại, nếu cấp nhanh, quá trình xả nguyên liệu bị cản trở, thời gian nguyên liệu ở trong buồng xay lâu hơn, sẽ có nhiều tiểu phân nhỏ được tạo ra. Tuy nhiên, quá trình này làm tiêu tốn thêm nhiều năng lượng và thường áp dụng với lượng nhỏ nguyên liệu, xay một lần. Tốc độ xả nguyên liệu nên cân bằng với tốc độ cấp liệu, quá trình nghiền sẽ hiệu quả hơn.
Bản chất của vật liệu nghiền xác định quá trình nghiền. Các vật liệu dạng sợi không thể bị nghiền bằng lực va chạm mà phải bị cắt. Trong khi đó, các vật liệu bở vụn lại có thể bị nghiền nhờ ma sát hoặc va chạm.
Sự có mặt của một lượng nhỏ nước (khoảng 5%) làm cản trở quá trình nghiền do tạo khôi dính bết, đặc biệt với các vật liệu đã có sẵn độ mịn nhất định. Vì vậy, cần lưu ý khi vật liệu nghiền là các muối ngậm nước (ví dụ Na2S04.H20), các muối hút ẩm (ví dụ CaCl2) hoặc nghiền trong môi trường có độ ẩm cao. Tuy nhiên, với hàm lượng nước lớn hơn 50%, khối vật liệu thành bột nhão. Quá trình trở thành nghiền ướt và vật liệu sau nghiền thường mịn hơn.
Nhiệt sinh ra trong quá trình nghiền cũng có thể làm ảnh hưởng đến vật liệu, đặc biệt là những vật liệu có nhiệt độ nóng chảy thấp, như gôm tổng hợp, sáp, nhựa cây. Những thuốc nhạy cảm với nhiệt cũng có thể bị hỏng. Một số chất màu có thể thay đổi màu nếu nhiệt độ cao. Những vật liệu không bền và phần lớn những vật liệu mịn có thể gây cháy nổ nếu nhiệt độ cao.
1.3. Các thiết bị xay, nghiền
Một thiết bị xay nghiền thông thường gồm 3 bộ phận: bộ phận cấp nguyên liệu, bộ phận nghiền và bộ phận thu nguyên liệu. Lực tác động sử dụng trong các thiết bi bị xay có thể là: lực nén ép, lực cắt, lực mài mòn hoặc phối hợp của các lực trên. Những loại máy nghiền thông dụng nhất trong công nghiệp dược gồm: máy nghiền cắt, nghiền búa, nghiền bi và nghiền năng lượng cao.
Phần lớn các loại máy này được thiết kế cho quá trình tháo nguyên liệu nhờ trọng lực. Với riêng loại máy nghiền năng lượng cao, người ta sử dụng thay thế bằng dòng khí mang.
Một điểm cần chú ý khi sử dụng thiết bị xay, nghiền là khả năng nhiễm tạp do mài mòn thiết bị. Quá trình xay càng kéo dài thì khả năng nguyên liệu bị nhiễm tạp càng lớn.
1.3.1. Máy nghiền cắt
Dùng xay, nghiền các vật liệu dai, dạng sợi. Lực cơ học sử dụng là lực cắt. Máy nghiền cấu tạo bởi 2 hệ thống dao cắt, một hệ thống gắn với trục chuyên động nằm ngang, hệ thống còn lại gắn với vỏ máy đứng yên. Trong quá trình nghiền, tiểu phân bị vỡ ra dưới tác động của hai hệ thống dao cắt. Phía bên dưới vỏ máy có đặt một lưới rây nhằm giữ lại các tiểu phân có kích thước lớn. Các tiểu phân này tiếp tục bị nghiền bởi hệ thông dao cho tới khi nhỏ hơn mắt rây.
Vật liệu nghiền ban đầu nên có kích thước nhỏ hơn chiều dài của dao cắt. ở điều kiện hoạt động tối ưu, máy có thể nghiền vật liệu tới kích thước khoảng 100µm.
1.3.2. Máy nghiền búa
Nghiền búa là thiết bị sử dụng lực va chạm để làm giảm kích thước tiểu phân. Máy cấu tạo gồm nhiều búa được gắn trên một trục quay với tốc độ cao (10.000 vòng/phút). Nguyên liệu sau khi được nạp vào máy sẽ quay theo chiều quay của trục, va chạm với các búa hoặc đập vào thành máy, cuối cùng vỡ ra thành các tiểu phân nhỏ hơn. Do tốc độ va chạm lớn, phần lớn các vật liệu đáp ứng kiểu giòn.
Theo thời gian, kích thước tiểu phân giảm, quán tính của các tiểu phân va chạm với búa cũng giảm một cách rõ rệt. Do đó quá trình tiếp tục làm vỡ tiểu phân kém hơn. Máy xay búa có xu hướng tạo ra phân bố kích thước tiểu phân hẹp.
Bên dưới vỏ máy cũng bố trí các lưới rây để kiểm soát kích thước tiểu phân đầu ra. Các tiểu phan đi qua rây có thể có kích thước nhỏ hơn nhiều so với kích thước mắt rây do các tiểu phân chuyển động đến mặt rây theo phương tiếp tuyến.
Nghiền búa là loại thiết bị nghiền rất phổ biến trong công nghiệp dược phẩm do có thể nghiền được rất nhiều loại vật liệu, gồm cả vật liệu khô và ướt. Giới hạn kích thước mà nghiền búa có thể đạt tối là khoảng vài chục micromet. Có thể điều chỉnh kích thước sản phẩm đầu ra nhờ điều chỉnh tốc độ quay của búa và kích thước mắt rây.
1.3.3. Máy nghiền bi
Nghiên bi là ví dụ của phương pháp nghiền kết hợp lực va chạm và lực ma sát giữa các tiểu phân. Máy nghiền gồm một thùng rỗng hình trụ có thể quay quanh trục nằm ngang. Thùng chứa được nạp bi khoảng 30-50% thể tích, thường gồm nhiều loại bi có kích thước khác nhau nhằm cải thiện chất lượng sản phẩm do các viên bi lớn có xu hướng tác động vào các nguyên liệu thô đầu vào, còn các viên bi nhỏ làm mịn tiểu phân.
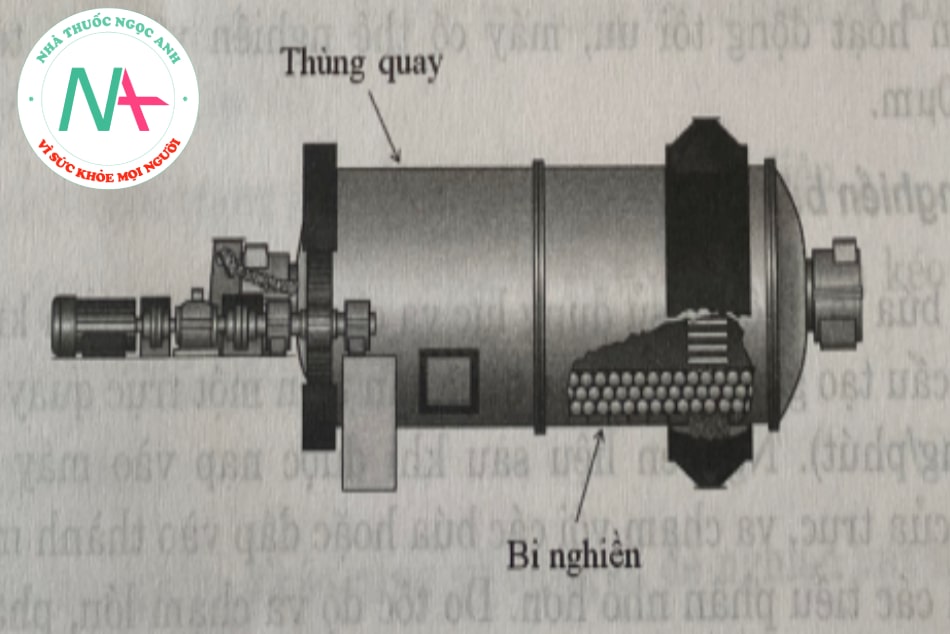
Số lượng nguyên liệu trong máy có ý nghĩa quan trọng: quá nhiều nguyên liệu tạo hiệu ứng đệm, quá ít nguyên liệu làm giảm hiệu suất và làm mài mòn vỏ máy.
Yếu tố ảnh hưởng quan trọng nhất đến quá trình làm việc của máy là tốc độ quay.
– Tại tốc độ thấp, lực ma sát kéo các viên bi chuyển động lên cao và trượt xuống do tác động của trọng lực. Quá trình lặp lại liên tục, chuyển động của bi rất ít nên làm giảm kích thước không đáng kể.
– Tại tốc độ cao, các viên bi do tác động của lực ly tâm, sẽ dính vào thành máy và không gây ra sự va chạm để làm giảm kích thước tiểu phân.
– Ở tốc độ vừa phải (khoảng 2/3 tốc độ làm bi dính vào thành máy), tác động nối tầng diễn ra. Các viên bi được đưa lên cao rồi rơi xuống tạo nên va chạm rất mạnh. Tốc độ tối ưu của quá trình quay phụ thuộc vào đường kính máy xay.
Nghiên bi là loại thiết bị sử dụng để nghiền mịn, nó có một số ưu điểm như:
– Nghiền được bột rất mịn (cỡ vài chục nm).
– Là thiết bị nghiền kín nên có thể sử dụng để nghiền cả khô và ướt, nghiền trong môi trường khí trơ.
– Có thể duy trì được trạng thái vô khuẩn của nguyên liệu.
Tuy nhiên thiết bị này có nhược điểm là thời gian nghiền kéo dài và vì thế dễ làm tăng tạp trong nguyên liệu.
1.3.4. Máy nghiến rung
Một loại thiết bị nghiền khác cũng sử dụng bi để nghiền vật liệu là máy nghiên rung.
Máy được nạp khoảng 80-90% thể tích bởi các viên bi sắt hoặc sứ. Trong quá trình nghiền, máy sẽ rung và sự va chạm với các viên bi làm giảm kích thước tiểu phân. Các tiểu phân có kích thước nhỏ hơn kích thước mắt rây đặt phía dưới máy sẽ chui ra khỏi máy.
Hiệu suất nghiền của máy nghiền rung cao hơn so với máy nghiền bi truyền thống.
1.3.5. Thiết bị xay kiểu đĩa răng
Thiết bị có cấu tạo gồm hai đĩa tròn đặt thẳng đứng, song song với nhau, trên mỗi đĩa gồm nhiều răng được sắp xếp theo các vòng đông tâm, xen kẽ (hình 1.6). Trong quá trình quay rất nhanh, dưới tác động của lực ly tâm, các tiểu phân va chạm và ma sát với các đĩa răng để giảm kích thước.
Khi thiết bị hoạt động, vật liệu được nạp liên tục vào khoang giữa hai đĩa tròn. Tùy vào từng loại thiết bị, có thể một hoặc cả hai đĩa chuyến động. Trong trường hợp cả hai đĩa chuyển động, đĩa thứ hai chuyển động ngược chiều so với đĩa thứ nhất. Ngoài va chạm với các đĩa răng, các tiếu phân trước khi thoát ra ngoài còn có thể bị làm nhỏ bằng cách va chạm với các răng cố định hoặc phải vượt qua lưới rây định cỡ đặt bên dưới thiết bị. Nhiệt sinh ra trong quá trình nghiền có thể được làm mát bằng luồng hệ thông khí. Các khí này ngoài ra còn giúp các tiểu phân không bị đọng lại giữa các đĩa răng.
Ưu điểm:
– Nghiền mịn các tiểu phân với năng lượng tiêu thụ hợp lý.
– Độ ồn nhỏ.
Nhược điểm:
– Phân bố kích thước tiểu phân hẹp.
– Có thể phải cần hệ thống làm mát.
1.3.6. Máy nghiền năng lượng cao
Để làm nhỏ kích thước nguyên liệu xuống mức thấp (1-20 µm), thường phải sử dụng các máy nghiền năng lượng cao. Nguyên lý hoạt động của loại thiết bị này được mô tả trên hình 1.7. Thiết bị nghiền hình dạng ống rỗng có đường kính 20-200 mm. Dòng khí được thổi vào từ đáy thiết bị với áp lực cao, gặp các tiểu phân sẽ tạo nên một vùng hỗn loạn, ở đó các tiểu phân va chạm với nhau. Khi sự va chạm đủ mạnh, tiểu phân sẽ bị gãy vỡ. Các tiểu phân có kích thước đủ mịn, sẽ bị hút theo dòng khí, chuyển động trong thiết bị đến vị trí thoát ra của nguyên liệu.
1.4. Lựa chọn phương pháp nghiền
Các phương pháp nghiền khác nhau sẽ cho ra sản phẩm với tỉ lệ kích thước và hình dạng tiểu phân khác nhau, qua đó ảnh hưởng tới các đặc tính hóa lý của bột nghiền. Việc lựa chọn phương pháp nghiền phụ thuộc vào yêu cầu kích thước đầu ra và yếu tố kinh tế. Ngoài ra, còn căn cứ vào các yếu tố sau:
– Các yếu tố nguyên liệu (kích thước, hình dạng, độ ẩm, đặc tính hóa lý).
– Dung tích máy và tốc độ.
– Tính linh hoạt của quá trình (nghiền khô, ướt, thay đổi tốc độ và lưới rây).
– Kiểm soát bụi.
2. Rây
Rây là một trong những phương pháp cổ điển và đáng tin cậy nhất để đánh giá, phân loại kích thước tiểu phân. Ưu điểm chính của phương pháp là khả năng xử lý cùng lúc lượng lớn vật liệu, dễ thao tác, chi phí đầu tư và bảo trì cho thiết bị nhỏ. Tuy nhiên, nhược điểm là trong quá trình rây, lực tác động lên tiểu phân có thể gây mài mòn hoặc gãy vỡ, ảnh hưởng đến phân bố kích thước tiểu phân.
Quá trình rây nhằm phục vụ hai mục đích:
– Phân riêng hoặc phá vỡ kết tập tiểu phân trong khối bột thành kích thước mong muốn.
– Phân tích xác định kích thước tiểu phân.
Cần chú ý rằng cấu tạo rây cho mỗi loại mục đích này rất khác nhau. Rây phân tích kích thước không nên sử dụng để làm nhỏ phần kết tập tiểu phân do quá trình này có thể gây mài mòn lưỡi rây, nguy cơ gây sai số cho quá trình phân tích kích thước tiểu phân và ảnh hưởng đến kết quả thu được.
Quá trình phân tích kích thước được thực hiện khá đơn giản. Mẫu với khối lượng biết trước được đặt ở mặt trên rây, chịu tác động của các lực rây rung lắc hoặc luồng không khí, tiểu phân chuyển động xung quanh và có xu hướng đi xuống dưới xuyên qua mắt rây. Những tiểu phân nhỏ hơn kích thước mắt rây sẽ chui qua rây trong khi những tiểu phân có kích thước lớn hơn sẽ ở lại. Vì vậy, nếu một tiểu phân đi qua rây 125 µm nhưng bị giữ lại trên rây 75 µm thì kích thước tiểu phân nằm trong khoảng 75-125 µm. Thông thường, kích thước tiểu phân có thể được lượng giá bằng đường kính mắt rây nhỏ nhất mà tiểu phân đó có thể chui qua. Chú ý rằng nếu tiểu phân có hình dạng dài (hình kim) kích thước thu được từ phân tích rây có thể không đại diện cho kích thước thực của tiểu phân.
Sử dụng một hệ thống lưới rây với mức độ tăng dần của kích thước mắt rây có thể tách riêng được mẫu bột thành các kích thước khác nhau. Từ đó, người ta có thể vẽ được phân bố kích thước tiểu phân theo khối lượng. Phương pháp này có một số nhược điểm như:
– Chỉ sử dụng để đánh giá các loại bột có kích thước tiểu phân lớn hơn 50 µm, nếu kích thước nhỏ hơn cần thực hiện trong điều kiện thiết bị kín (loại dùng khí đẩy hoặc trong môi trường lỏng để phân tán bột mịn).
– Khó đánh giá với các loại tiểu phân tích điện.
– Kích thước lưới rây khó đồng nhất, các điều kiện (như rung lắc) ảnh hưởng nhiều đến kết quả.
– Hình dạng tiểu phân ảnh hưởng đến kết quả.
2.1. Đặc điểm chung về rây
Rây thường được tạo nên từ các sợi kim loại đan vào nhau, với kích thước mắt rây dao động từ 20µm đến 125 mm. Trên thế giới, nhiều tiêu chuẩn về rây đã được đưa ra, khác nhau về cỡ rây và kích thước mắt rây. Trong phần lớn các trường hợp, cỡ rây có thể được xác định bởi kích thước mắt rây, số rây hoặc số mạng lưới. Tiêu chuẩn của Hiệp hội về thử nghiệm vật liệu của Mỹ (ASTM) quy định cỡ rây chính là số lượng dây kim loại trên chiều dài 1 inch (2,54 cm), trong khi đó, châu Âu quy định cỡ rây là kích thước thực của mắt rây. Ví dụ ở Mỹ rây số 45 (kí hiệu là #45) tức là trong 1 inch có 45 sợi dây kim loại đặt cách đều và kích thước mắt rây là 355 µm. Trong khi đó, ở châu Âu, kí hiệu #45 có nghĩa là kích thước mắt rây 45 µm.
Bên cạnh sự khác nhau về tên gọi, giữa các tiêu chuẩn còn có sự khác nhau về kích thước. Ví dụ kích thước mắt rây #12 và #14 theo ASTM lần lượt là 1,7 và 1,4 mm trong khi đó theo tiêu chuẩn của Nhật, #12 và #14 lần lượt tương đương với 1,4 và 1,18 mm. Do đó tiêu chuẩn sử dụng để phân tích kích thước tiểu phân phải được chỉ rõ nguồn gốc, tránh gây nhầm lẫn, đặc biệt là những sản phẩm lưu hành quốc tế.
Nhìn chung, có 3 kiểu cấu trúc rây: kiểu đan lưới, kiểu tấm đục lỗ và micromesh.
– Kiểu đan lưới có cấu tạo gồm nhiều dây kim loại bằng đồng hoặc thép không rỉ, được đặt trên một giá hình trụ rỗng. Dây kim loại có thể được đan trơn hoặc đan chéo. Các cách đan khác nhau này dẫn đến kích thước mắt rây cũng có sự khác nhau do sai khác về hình thái xung quanh mắt rây.
– Kiểu tấm: gồm nhiều lỗ được đục trên một tấm phẳng để tạo ra các mắt rây tròn. Do cấu trúc như vậy nên kiểu tấm khỏe hơn kiểu đan lưới.
– Kiểu micromesh: sử dụng phương pháp khắc ảnh để tạo mắt rây, trong đó kích thước mắt rây mong muốn được in lên một tấm kim loại và sau đó khắc theo hình ảnh được in.
Cần chú ý, các loại rây phải thường xuyên được kiểm tra để đảm bảo đồng nhất kích thước mắt rây và tránh có hỏng hóc trước khi làm thí nghiệm. Mọi lực tác động làm di chuyển dây kim loại trên mặt sẽ làm thay đổi kích thước mắt rây. Điều này đặc biệt cần lưu ý nếu sử dụng rây với mục đích phá vỡ kết tập tiểu phân.
2.2. Hiệu suất rây
Hiệu suất rây được định nghĩa là hiệu quả của quá trình phân tách tiểu phân lớn và tiểu phân nhỏ. Quá trình rây phân loại đạt hiệu suất 100% nếu tất cả những hạt có kích thước lớn hơn kích thước mắt rây sẽ nằm lại trên rây, các hạt nhỏ hơn kích thước lỗ rây sẽ đi qua rây. Thực tế sản xuất, quá trình rây phân loại không bao giờ đạt 100% do có một số hạt nhỏ hơn kích thước mắt rây vẫn nằm trên rây, một số lớn hơn kích thước mắt rây nhưng vẫn lọt qua.
Hiệu suất rây được tính bằng tỷ số giữa lượng hạt lọt qua rây với lượng hạt có kích thước nhỏ hơn mắt rây:
H=(m1.100%)/m.a
Trong đó: m1: khối lượng hạt thực tế dưới rây
m: khối lượng vật liệu cho vào rây
a: thành phần có kích thước nhỏ hơn mắt rây
Tùy theo kiểu và cấu tạo của rây, hiệu suất thường được thay đổi trong khoảng 10-75%, tối đa đạt 90%.
2.3. Một số yếu tố ảnh hưởng đến quá trình rây
Mặc dù rây là phương pháp đơn giản và tin cậy, cần chú ý một số thông số sau trong quá trình rây để đạt được kết quả lặp lại: đặc điểm rây, chuyển động của rây, đặc tính bột, thời gian rây và khối lượng mẫu.
2.3.1. Đặc điểm rây
Yếu tố đầu tiên được đề cập đến là cỡ rây. Có nhiều loại cỡ rây ứng với các kích thước mắt rây khác nhau, trong đó mỗi cỡ rây xác định kích thước tiểu phân mà nó cho qua. Nếu như không lựa chọn đúng loại cỡ rây, chúng ta có thể nhận định sai lầm về kích thước tiểu phân. Ví dụ, sử dụng hai rây có kích thước 180 µm và 90 µm để phân tích kích thước vật liệu có đường kính trung bình 100 µm. Phần lớn lượng vật liệu đi qua rây 180 trong khi chỉ có một phần nhỏ đi qua rây 90 dễ dẫn đến kết luận kích thước trung bình mẫu là 180 µm. Chính vì vậy, điều quan trọng là phải lựa chọn đúng loại rây đại diện tốt cho kích thước tiểu phân.
Người ta khuyến cáo nên lựa chọn hệ thống lưới rây có kích thước mắt rây cách nhau √2 lần để có thể bao phủ toàn bộ các khoảng kích thước. Trở lại ví dụ với vật liệu có đường kính trung bình 100 µm, sử dụng bộ 6 rây với các kích thước 45, 63, 90, 125, 180 và 250 µm sẽ cho kết quả sơ bộ về phân bố kích thước tiểu phân. Khi đã biết được sơ bộ kích thước và phân bố kích thước tiểu phân rộng hay hẹp, người ta có thể tiếp tục lựa chọn rây để tối ưu phương pháp. Ngoài ra, trước khi sử dụng rây có thể dùng kính hiển vi để xác định kích thước, giúp chọn rây hợp lý hơn.
Vật liệu làm rây cũng có vai trò quan trọng. Cần chú ý mẫu phân tích không phản ứng với vật liệu làm rây để tránh những kết quả bất ngờ có thể xảy ra làm thay đổi kích thước hoặc hình dạng tiểu phân. Việc hiệu chỉnh rây nên được thực hiện thường xuyên để đảm bảo thu được dữ liệu chính xác.
2.3.2. Chuyển động của rây và đặc tính bột
Quá trình rây có thể bị ảnh hưởng khi các tiểu phân bít kín mắt rây. Điểu này làm giảm hiệu suất rây, đặc biệt ở các rây cỡ nhỏ. Mặt khác, nếu hình dạng tiểu phân khác thường, như hình dài hoặc hình kim, việc bít kín lỗ rây còn nguy hại hơn do những tiểu phân này có thể bị giữ lại trong suốt quá trình thao tác. Để hạn chế hiện tượng bít mắt rây, có thể làm chuyển động bề mặt rây như trong các thiết bị rây tự động. Tuy nhiên, nếu dùng lực quá mạnh có thể làm vỡ tiêu phân dẫn đến quá trình đánh giá kích thước không còn chính xác. Vì vậy, cần xem xét cân bằng giữa hiệu suất rây và đặc tính tiểu phân khi lựa chọn thiết bị.
Đôi khi trong quá trình rây, mẫu phân tích không chuyển động, các tiểu phân dính vào thành rây hoặc có xu hướng kết tập lại thành những tiểu phân lớn hơn. Trong trường hợp này có thể thêm một vài tá dược trơn như talc, Aerosil, acid béo để làm giảm sự kết dính các tiểu phân.
2.3.3. Thời gian rây và khối lượng mẫu
Thời điểm kết thúc rây phụ thuộc phần lớn vào khối lượng mẫu. Nếu mẫu lớn, số lượng tiểu phân trên một mắt rây tăng lên, thời gian phân tích phải lâu hơn. Tuy nhiên, việc tăng thời gian phân tích sẽ làm tăng nguy cơ tiểu phân bị mài mòn và ảnh hưởng đến phân bố kích thước.
Để xác định điểm kết thúc trong phân tích kích thước tiểu phân, ban đầu người ta chạy thí nghiệm trong 5 phút, sau đó cẩn thận gỡ bỏ các lưới rây, cân phần bột trên rây mà không làm mất khối lượng. Sau đó, quá trình được thực hiện lại trong 5 phút. Theo Dược điển Mỹ, quá trình phân tích được coi là kết thúc nếu lượng bột cân được trên rây không chênh lệch quá 5% hoặc 0,1 g so với lượng trên rây được thực hiện ở thí nghiệm trước. Nếu sự sai khác lớn hơn 5%, cần phải thực hiện thí nghiệm ở thời gian lâu hơn.
2.4. Thiết bị rây
Các thiết bị rây khác nhau ở cách làm chuyển động tiểu phân, dựa vào lực cơ học hoặc luồng không khí dao động. Các lực cơ học có thể là lực xoay tròn, lắc, gõ hoặc rung, thường tác động mạnh tới tiểu phân và dễ gây mài mòn. Trong khi đó phương pháp sử dụng luồng không khí dao động làm tiểu phân chuyển động rất hiệu quả, ít gây mòn tiểu phân, đồng thời hạn chế khả năng vật liệu bít mắt rây.
Một hệ thông rây phân tích thường sử dụng ít nhất 2 rây với kích thước mắt ray khác nhau. Rây cỡ lớn nhất được đặt ở trên cùng, lần lượt phía dưới là các rây theo thứ tự kích thước mắt rây nhỏ dần. Các tiểu phân chịu tác động của lực rây có xu hướng lọt qua lưới rây nếu kích thước nhỏ hơn kích thước rây và được giữ lại nếu kích thước lớn hơn. Việc xác định khối lượng mẫu bột trên bề mặt rây sau khi quá trình kết thúc cho phép xây dựng phân bố kích thước tiểu phân theo khối lượng.
2.4.1. Thiết bị rây dùng lực cơ học
Điển hình trong các thiết bị rây loại này là máy rây rung. Máy hoạt động nhờ một hệ thông lò xo rung đặt dưới các lưới rây. Các tiểu phân phía trên lưới rây sẽ tham gia liên tiếp ba chuyển động: tiểu phân được gia tốc theo phương thẳng đứng hướng lên trên với biên độ vài mm, tiểu phân quay tròn tự do trên không trung, sau đó rơi trở lại mặt rây nhờ trọng lực. Do tham gia kết hợp nhiều chuyển động nên các tiểu phân được trải đều khắp bề mặt rây. Hiệu suất rây nhờ đó được tăng lên đáng kể.
Ngoài rây rung, một số thiết bị rây chỉ sử dụng chuyển động xoay tròn hoặc kết hợp chuyển động tròn với lực gõ theo hướng trục rây để thực hiện quá trình (hình 1.11). Các tiểu phân trên bề mặt rây do ít tham gia chuyển động hơn nên ít khi thay đổi hướng, thời gian rây cũng lâu hơn so với thiết bị rây rung. Bên cạnh đó, lực gõ mạnh khiến các tiểu phân dễ bị mài mòn, sinh ra nhiều tiểu phân mịn.
2.4.2. Thiết bị rây dùng khí
Khác với các thiết bị rây dùng lực cơ học, ở đây, luồng không khí được sử dụng làm chuyển động các tiểu phân. Hai thiết bị rây điển hình thuộc loại này là air jet và sonic sifter.
2.4.2.1. Thiết bị rây kiểu Air jet
Thiết bị cấu tạo gồm một buồng rây được kết nối với một bơm chân không (hình 1.11). Áp suất âm khiến không khí được hút vào buồng qua một khe có khả năng chuyển động xoay tròn. Khi đi qua khe hẹp, luồng không khí được tăng tốc và thổi vào bề mặt rây, làm chuyển động các vật liệu trên rây. Các tiểu phân có kích thước phù hợp, lọt qua lưới rây và được hút vào bộ phận thu hồi.
Ưu điểm của thiết là ở khả năng hạn chế bít lỗ rây. Các lực tác động rất nhẹ nhàng nên ít có khả năng gây vỡ tiểu phân; có thể dùng với các tiểu phân rất mịn (cỡ 10 µm) và khả năng lặp lại kết quả rất cao. Tuy nhiên, trong một thời điểm, máy chỉ hoạt động với một lưới dây duy nhất. Nếu cần phân tích kích thước, quá trình cần được lặp lại qua nhiều lưới rây có kích thước khác nhau.
2.4.2.2. Thiết bị rây kiểu Sonic sifter
Là một trong những thiết bị rây phổ biến và hiệu quả sử dụng cột không khí dao động làm chuyển động tiểu phân và lực rung theo chiều dọc để tách kết tập tiểu phân. Thiết bị cho phép phân loại các tiểu phân trong khoảng từ 20 – 2000 µm với hầu hết các vật liệu. Quá trình rây được thực hiện nhanh và ít gây ra tiếng ồn.
Thiết bị có thể hoạt động dưới hai chế độ: rây hoặc rây rung. Điều này cho phép người dùng tối ưu hóa quá trình phân tích cho những tiểu phân có tỉ trọng khác nhau. Nếu sử dụng đồng thời cả rây và rung, lực theo chiều dọc sẽ tác động vào hệ thống rây sau những khoảng thời gian nhất định, để định hướng lại tiểu phân và làm vỡ một cách nhẹ nhàng những tiểu phân bám dính hoặc kết tập. Bên cạnh đó, thiết bị còn có thể điều chỉnh cường độ rung và thời gian rung.
Khi thực hiện phân tích kích thước tiểu phân qua rây, chú ý rằng biên độ dao động không nên quá lớn bởi các tiểu phân khi nảy lên cao sẽ có xu hướng bay xung quanh chứ không chui qua rây. Mặt khác, nếu biên độ quá nhỏ, tiểu phân sẽ chỉ va đập trên bề mặt rây có thể dẫn đến bị mòn. Do vậy, cần phải lựa chọn phương pháp tối ưu cho các tiểu phân có các đặc tính khác nhau để đạt được kết quả tốt.
Câu hỏi lượng giá
1. Vai trò của quá trình xay, nghiền trong công nghiệp dược phẩm?
2. Các yếu tố ảnh hưởng đến quá trình xay, nghiền?
3. Cấu tạo, nguyên tắc hoạt động, ưu nhược điểm và ứng dụng của các thiết bị xay, nghiền về?
4. Mục đích quá trình rây?
5. Các yếu tố ảnh hưởng đến quá trình rây?
6. Cấu tạo, nguyên tắc hoạt động, ưu nhược điểm và ứng dụng trong công nghiệp dược phẩm của các thiết bị rây?