Tác giả: Tiến sĩ Dược sĩ Nguyễn Phúc Nghĩa.
Bài viết Trộn là gì? Vai trò của quá trình trộn trong sản xuất thuốc trích trong chương 2 sách Một số quá trình và thiết bị trong công nghệ dược phẩm – giáo trình đào tạo dược sĩ đại học bộ môn Công Nghiệp Dược trường Đại học Dược Hà Nội.
Mục tiêu học tập
- Trình bày được vai trò của quá trình trộn trong sản xuất thuốc.
- Trình bày được lý thuyết quá trình trộn.
- Trình bày được các kỹ thuật và thiết bị trộn trong sản xuất thuốc.
Trộn là quá trình phân bố ngẫu nhiên các tiểu phân khác loại trong cùng một hệ. Nó khác với một hệ trật tự, ở đó các tiểu phân được sắp xếp theo nguyên tắc lặp lại. Đây là một trong những quá trình được sử dụng nhiều nhất trong cuộc sống hàng ngày. Trong công nghiệp dược phẩm, trộn là quá trình cơ bản do hiếm khi thuốc có cấu tạo từ một thành phần duy nhất.
1. Đại cương
1.1. Khái niệm về quá trình trộn
Để hiểu được diễn biến quá trình trộn, hãy xem xét tình huống đơn giản nhất, khi trộn hai khối bột giống hệt nhau về số lượng, kích thước, hình dạng và tỷ trọng các tiểu phân; sự khác biệt duy nhất là màu sắc. Hình dung quá trình trộn giông như quá trình sắp xếp xen kẽ các ô vuông đen trắng trên hình 2.1a.
Theo lý thuyết, quá trình trộn lý tưởng xảy ra khi mỗi tiểu phân thuộc nhóm này nằm liền kề với một tiểu phân thuộc nhóm khác (hình 2.1b). Tuy nhiên, trường hợp này hầu như không thể xảy ra. Nói cách khác, xác suất để trường hợp (b) xảy ra rất nhỏ, bằng với xác suất khối bột trở lại trạng thái ban đầu (a) sau một thời gian trộn.
Thực tế, quá trình trộn thường diễn ra như trong trường hợp (c), ở đó các tiểu phân không nhất thiết nằm xen kẽ nhau, mà phân bố sao cho xác suất lựa chọn được một loại tiểu phân nhất định (ô đen hoặc ô trắng) bằng nhau ở mọi vị trí và bằng với xác suất lựa chọn các tiểu phân đó trong toàn hỗn hợp. Ví dụ trong trường hợp các ô vuông, nếu chia hỗn hợp thành các cụm gồm 16 ô vuông nhỏ, xác suất để lấy được ô đen trong một cụm bất kì là 0,5 bằng với xác suất để lấy được ô đen trong toàn hỗn hợp.
Trong một hỗn hợp, các thành phần có thể coi là đã trộn lẫn với nhau nếu hàm lượng từng thành phần lấy ra trong một mẫu bất kỳ tương đương nhau.
1.2. Các đại lượng thống kê của hỗn hợp
Thực tế, hàm lượng các thành phần trong mẫu được lấy ra ở các vị trí khác nhau trong hỗn hợp đã trộn không bao giờ đồng nhất. Mục tiêu của quá trình thiết kế và thực hiện trộn là làm giảm sự dao động này xuống mức chấp nhận được.
Trở lại với tình huống trộn hỗn hợp gồm hai thành phần giống nhau về kích thước, hình dạng và tỉ trọng các tiểu phân. Độ lệch chuẩn (SD) của hàm lượng thành phần A trong mẫu so với hàm lượng trung bình được tính toán theo công thức :
SD=√(p(1-p)/p)
Trong đó:
p là hàm lượng của thành phần A trong hỗn hợp
n là số lượng tiểu phân trong mẫu.
Phương trình trên cho thấy khi tăng số lượng tiểu phân trong mẫu thì SD giảm, điều đó có nghĩa là sự dao động về hàm lượng thành phần A trong mẫu cũng giảm.
Một thông số hữu ích khác cần xác định để đánh giá quá trình trộn là hệ số biến thiên (CV) hay độ lệch chuẩn tương đôi (RSD) của thành phần A:
RSD (%)= CV(%)= (SD/p)*100
Hệ số biến thiên sẽ giảm khi hàm lượng p của thành phần A trong hỗn hợp tăng lên. Trong ngành dược, tỉ lệ dược chất thường không lệch quá 5% so với hàm lượng trung bình.
1.3 Đánh giá quá trình trộn
Để đánh giá quá trình trộn một hỗn hợp, giả sử gồm dược chất với tá dược, thường sử dụng phương pháp định lượng hàm lượng dược chất trong các mẫu lấy tại các vị trí khác nhau trong thiết bị trộn. Từ các kết quả định lượng thu được, tính độ lệch chuẩn tương đối để đánh giá mức độ đồng đều giữa các mẫu. Độ lệch chuẩn tương đối càng nhỏ phản ánh mức độ đồng nhất của quá trình trộn càng cao.
Có hai vấn đề cần chú ý trong việc lấy mẫu. Đó là số lượng mẫu cần lấy và khối lượng mỗi mẫu. Số lượng mẫu lấy phải đủ nhiều để đại diện cho hỗn hợp (ít nhất 6 mẫu), mẫu phải được lấy ở các vị trí nông sâu khác nhau, và khi lấy mẫu không làm ảnh hưởng quá nhiều đến hỗn hợp. Về vấn đề khối lượng mẫu, mẫu đánh giá thường có khối lượng từ 1 đến 3 lần khối lượng của một đơn vị liều bào chế (ví dụ khối lượng của mẫu bằng khối lượng của một viên bào chế).
2. Trộn chất rắn
2.1. Cơ chế của quá trình trộn rắn
Để quá trình trộn chất rắn có thể diễn ra cần sự chuyển động tương đối giữa các tiểu phân. Có ba cơ chế chính mà các tiểu phân trộn lẫn với nhau gồm đối lưu, khuếch tán và chia cắt.
2.1.1. Trộn đối lưu
Trộn đối lưu diễn ra khi có sự chuyển dịch của các nhóm tiểu phân từ vị trí này sang vị trí khác trong khối bột. Do chỉ có sự dịch chuyển theo nhóm tiểu phân nên quá trình là trộn thô và diễn ra khá nhanh. Để đạt được mức độ phân bố ngẫu nhiên của từng tiểu phân thì cần tăng thời gian trộn.
2.1.2. Biến dạng (chia cắt)
Trộn kiểu chia cắt diễn ra khi một lớp vật liệu chuyển động trượt trên các lớp vật liệu khác. Đó là do trong quá trình trộn, vận tốc giữa các lớp không đồng nhất và dần khác nhau trong khối bột.
2.1.3. Trộn khuyếch tán
Trộn khuếch tán là sự chuyển động ngẫu nhiên làm thay đổi vị trí tương đối của các tiểu phân trong khối bột. Khi tác động một lực để làm chuyển động khối bột, thể tích chiếm chỗ của khối bột tăng lên, các tiểu phân trở nên ít bị nén hơn, hình thành nên các lỗ xốp. Dưới tác động của trọng lực, các tiểu phân sau đó có xu hướng rơi xuống qua các lỗ xốp, và quá trình cứ tiếp tục như vậy khiến từng tiểu phân được di chuyển.
Khuyếch tán đôi khi được hiểu như là quá trình trộn vi mô, trong khi đó đối lưu được hiểu như là một quá trình trộn vĩ mô. Tất cả các cơ chế trên tác động đồng thời với mức độ khác nhau trong quá trình trộn và mức độ tác động từng loại thay đổi theo từng thiết bị.
2.1.4. Diễn biến của quá trình trộn
Khi quá trình trộn diễn ra, khối bột lần lượt trải qua bốn giai đoạn chính:
- Khôi bột rắn giãn nở về thể tích.
- Cơ chế trộn chia cắt bắt đầu xuất hiện trong khối bột, phụ thuộc vào hình dạng và cấu tạo máy trộn.
- Khối bột được nhào trộn đủ để các tiểu phân phân bố một cách ngẫu nhiên.
- Sự phân bố ngẫu nhiên của các tiểu phân được duy trì sau khi quá trình trộn kết thúc.
Ban đầu, các thành phần trộn mới được nạp vào máy, lực nén sinh ra do trọng lượng khối bột khiến chúng ở trạng thái tĩnh. Sau đó, khi máy trộn bắt đầu hoạt động, các lực cơ học tác động làm “giãn nở” khối bột trộn. Sự giãn nở này tạo ra các lỗ trống qua đó làm tăng chuyển động giữa các tiếu phân và hỗ trợ cho quá trình trộn. Nếu khối bột không giãn nở tăng thể tích, sự chuyển động của các tiểu phân bị giới hạn, dẫn đến thời gian trộn bị kéo dài và quá trình trộn có thể không được hoàn thiện. Vì lí do này, máy trộn chỉ nên nạp đầy tới 65-75% thể tích.
Một khi chuyển động của các tiểu phân được hình thành nhờ sự giãn nở thể tích của khối bột, sự chênh lệch về tốc độ giữa các phần trong khối bột càng làm tăng cường quá trình trộn. Cùng với đó, các lực nén, giãn và chia cắt tác động lên khối bột tạo nên chuyển động ngẫu nhiên của các tiểu phân. Nếu lực chia cắt không đủ để thắng lực hấp dẫn giữa các tiểu phân, sự kết tập tiểu phân có thể xảy ra dẫn đến quá trình trộn không hoàn tất.
2.3. Các yếu tố ảnh hưởng đến quá trình trộn
2.3.1. Kích thước, hình dạng và tỉ trọng các tiểu phân
Các tiểu phân, đặc biệt là các tiểu phân dược chất có hàm lượng nhỏ, thường được nghiền đến kích thước nhất định nhằm làm tăng số lượng tiểu phân trên một đơn vị khối lượng, góp phần cải thiện độ đồng đều hàm lượng dược chất trong hỗn hợp bột. Điều này hạn chế một số trường hợp chỉ có vài tiểu phân lớn phân bố trong khối bột, khiến quá trình trộn khó đồng nhất, ảnh hưởng đến độ đồng đều phân liều. Bên cạnh đó, quá trình nghiền còn nhằm tách các nhóm tiểu phân khỏi sự kết tập.
Hình dạng tiểu phân cũng ảnh hưởng đến quá trình trộn. Thường các tiểu phân có hình cầu hoặc hình khối có khả năng chảy tốt hơn nên hỗ trợ cho quá trình trộn. Ngược lại, các tiểu phân dạng tấm mỏng hoặc hình kim có khả năng chảy kém nên khó trộn hơn, dễ làm kết tập tiểu phân.
Tỉ trọng các thành phần bột trộn nên tương tự nhau bởi nếu không sẽ rất dễ dẫn đến hiện tượng phân lớp.
2.3.2. Lực kết dính
Một khối bột kết dính được định nghĩa là khối bột có lực hút giữa các tiểu phân (lực cơ học, tĩnh điện, van der Walls, sức căng bề mặt) lớn hơn khối lượng của tiểu phân ít nhất 10 lần. Cường độ lực kết dính giữa các tiểu phân chịu ảnh hưởng lớn từ các đặc tính vật lý của tiểu phân như kích thước, hình dạng, dạng thù hình và độ ẩm.
Lực kết dính trong khối bột nhỏ sẽ thúc đẩy quá trình trộn diễn ra nhanh hơn và các thành phần phân bố đồng đều hơn. Ngược lại, nếu lực kết dính quá cao, quá trình trộn rất khó diễn ra. Khi khối bột có lực kết dính, thường phải cần thêm lực tác động bên ngoài để đạt được sự đồng nhất. Lực tác động vừa có vai trò làm giãn nở khối bột vừa để phá vỡ kết tập tiểu phân. Phần lớn các vấn đề liên quan đến sự đồng đều trong quá trình trộn là kết quả của lực chia cắt thấp.
2.3.3. Độ ẩm và nhiệt độ
Độ ẩm có ảnh hưởng lớn đến khả năng liên kết giữa các tiểu phân trong vật liệu. Độ ẩm cao góp phần đẩy nhanh quá trình hình thành kết tập tiểu phân, trong đó độ ẩm bề mặt đóng vai trò quan trọng và có tác động mạnh hơn cả khả năng hút ẩm của vật liệu. Đối với những vật liệu này, thời gian trộn tối ưu phải được xác định sao cho khối bột có độ đều nhất chấp nhận được đồng thời hạn chế hút ẩm từ môi trường.
Nhiệt độ ảnh hưởng đến độ kết dính và xu hướng tạo kết tập tiểu phân. Mặc dù phần lớn quá trình trộn diễn ra ở nhiệt độ phòng, nhưng quá trình chuyển động giữa các tiểu phân có thể sinh nhiệt. Trong một số trường hợp, nhiệt có thể làm mềm tiểu phân và tăng khả năng dính lên thành thiết bị. Do vậy, có thể phải làm mát buồng trộn để giữ vật liệu dưới nhiệt độ hóa mềm.
2.3.4. Tốc độ chuyển động của thùng trộn
Tốc độ quay của thùng trộn có thể ảnh hưởng đến quá trình trộn, ở tốc độ trộn thấp, khối bột có hiện tượng chảy gián đoạn, tức là có những điểm bắt đầu chuyển động trong khi những điểm khác đã dừng lại. Khi tốc độ quay tăng lên, khối bột chảy đều hơn. Nếu tiếp tục tăng, quán tính lớn khiến tiểu phân bị dính vào thành thiết bị, do đó hạn chế khả năng chuyển động. Tốc độ quay còn ảnh hưởng đến lực chia cắt, qua đó ảnh hưởng đến hiệu quả trộn, đặc biệt khi trộn những vật liệu kết dính.
2.3.5. Tương tác tĩnh điện
Khi hai bề mặt tiếp xúc với nhau, sự trao đổi electron có thể khiến một bề mặt tích điện dương và bề mặt kia tích điện âm. Quá trình này gọi là điện ma sát. Chuyển động tương đối giữa các tiểu phân và sự va chạm với các bề mặt thiết bị trong các khi trộn, nạp, tháo nguyên liệu là những điều kiện lý tưởng cho quá trình điện ma sát xảy ra.
Tương tác tĩnh điện có thể khiến các tiểu phân kết tập với nhau hoặc tiểu phân dính lên thành máy. Ảnh hưởng của tương tác tĩnh điện có thể trở nên đặc biệt có ý nghĩa với những vật liệu có tỉ trọng thấp và điều kiện độ ẩm làm việc thấp.
2.4. Quá trình tách lớp
Tách lớp là quá trình ngược với trộn. Khi một khối vật liệu trộn bị tách lớp, phân bố ngẫu nhiên của các phần tử trở thành không ngẫu nhiên hoặc không bao giò trở nên ngẫu nhiên.
Quá trình tách lớp là do các tiểu phân cấu thành không có cùng hình dạng kích thước và tỷ trọng. Khi chịu cùng một lực tác động, các phần tử này sẽ đáp ứng không giống nhau và tách riêng. Những phần tử có cùng đặc tính sẽ tập hợp lại tạo nên những vùng có nồng độ cao hơn những vùng khác.
2.4.1. Kích thước tiểu phân
Sự khác biệt về kích thước là nguyên nhân chính dẫn đến hiện tượng phân lớp. Các tiểu phân nhỏ có xu hướng rơi qua các lỗ trống tạo ra bởi các phân tử lớn, xuống đáy của khối bột. Quá trình này có thể xảy ra ở khối bột tĩnh chứa nhiều tiểu phân có kích thước nhỏ, hoặc ở bất kì khôi bột nào chịu tác động của ngoại lực như rung, lắc, khuấy.
Một kiểu phân lớp khác liên quan đến chênh lệch về kích thước phân tử là do trong quá trình trộn, các phần tử có khối lượng lớn có xu hướng chuyển động xa hơn nhờ động năng lớn hơn. Kiểu phân lớp này khiến cho các tiểu phân lớn thường nằm ở rìa ngoài khối bột khi được đổ ra từ thùng chứa.
Ngoài ra, trong quá trình trộn hoặc quá trình tháo bột từ thùng chứa, các tiểu phân mịn dễ bị bay lên trong không trung tạo bụi mù do tác động của dòng khí hỗn loạn. Khi quá trình trộn dừng lại hoặc quá trình tháo bột đã kết thúc, các tiểu phân này dần lắng xuống, tạo nên một lớp màng mỏng bột trên bề mặt của những tiểu phân lớn.
2.4.2. Tỷ trọng bột
Nếu trong khối bột có thành phần tỷ trọng cao, nó sẽ có xu hướng chuyển động xuống dưới, mặc dù kích thước có thể tương đương nhau. Tương tự như vậy, thành phần tỉ trọng cao cũng chuyển động xa hơn thành phần tỉ trọng thấp có cùng kích thước. Tuy vậy, trong bào chế công nghiệp, thường tỷ trọng các loại bột không khác nhau nhiều nên ảnh hưởng của yếu tố này là không quá quan trọng.
2.4.3. Hình dạng tiểu phân
Hình dạng tiểu phân có liên quan đến diện tích bề mặt và khả năng bám dính giữa các tiểu phân. Tiểu phân hình cầu có diện tích bề mặt nhỏ nhất, khả năng trơn chảy tốt nhất nên rất dễ trộn và cũng rất dễ bị phân lớp. Các hình dạng khác với diện tích bề mặt lớn hơn, các tiểu phân có thể dính với nhau, giảm xu hướng phân lớp.
2.4.4. Phương pháp làm giảm sự phân lớp
- Lựa chọn kích thước tiểu phân, rây loại bỏ những tiểu phân quá mịn để thu được hỗn hợp tương đồng về kích thước.
- Sử dụng quá trình xay nghiền để làm hẹp phân bố kích thước tiểu phân hoặc đưa các tiểu phân về kích thước nhỏ (khoảng 30 µm), giúp quá trình phân lớp ít xảy ra hơn.
- Kiểm soát quá trình kết tinh để thu được cấu trúc tinh thể có hình dạng nhất định.
- Lựa chọn tá dược có tỷ trọng tương đương dược chất.
- Tạo hạt giúp tăng kích thước tiểu phân và tăng độ đồng đều hàm lượng.
- Tránh rung lắc hỗn hợp bột đã trộn.
- Sử dụng thiết bị có thể kết hợp nhiều quá trình tránh chuyển đổi các máy (ví dụ trộn tạo hạt tầng sôi).
- Thực hiện quá trình trộn thứ tự, giúp các tiểu phân có kích thước nhỏ sẽ được hấp phụ lên bề mặt tiểu phân lớn và do đó quá trình tách lớp được hạn chế.
2.5. Kỹ thuật trộn chất rắn
Khả năng trộn đều một hỗn hợp phụ thuộc vào tỷ lệ giữa các thành phần và kích thước tiểu phân của chúng. Nếu tỷ lệ dược chất – tá dược đủ lớn, chỉ cần trộn trực tiếp một giai đoạn là có thể thu được hỗn hợp đạt yêu cầu về đồng nhất.
Khi tỷ lệ dược chất nhỏ hơn 10%, trộn trực tiếp một giai đoạn không đảm bảo thu được hỗn hợp đồng nhất, khi đó cần phải trộn hai giai đoạn. Trước hết tạo hỗn hợp bột mẹ bằng cách trộn dược chất với một phần tá dược, sau đó sử dụng bột mẹ để trộn tiếp với phần tá dược còn lại.
Khi lượng dược chất nhỏ hơn 1%, kỹ thuật trộn hai giai đoạn cũng không thích hợp, khi đó hỗn hợp cần được trộn bằng kỹ thuật trộn đồng lượng. Phương pháp này còn được gọi là phương pháp trộn theo cấp số nhân, sử dụng nhiều trong phòng thí nghiệm.
Khi dược chất chiếm tỷ lệ nhỏ hơn nữa thì kỹ thuật trộn đồng lượng cũng không thích hợp. Khi đó, dược chất cần được hòa tan trong một dung môi thích hợp để trộn với hỗn hợp tá dược. Theo cách này, dịch lỏng được phân bố đều trên bề mặt các tiểu phân tá dược, về mặt lý thuyết đạt được độ đồng đều hàm lượng lý tưởng (RSD = 0 %).
2.6. Thiết bị trộn
Trong công nghiệp bào chế hiện nay, thiết bị trộn có thể được phân thành hai loại:
– Thiết bị trộn có thùng chứa chuyển động (thiết bị trộn tạo sự nhào lộn).
– Thiết bị trộn có thùng chứa tĩnh và các cánh trộn chuyển động.
Việc lựa chọn máy trộn nên là sự xem xét tổng hợp của các yếu tố sau đây:
– Các yếu tố liên quan đến vật liệu trộn như khả năng kết dính, sự kết tập tiểu phân, khả năng phân lớp trong quá trình trộn và quá trình tháo nguyên liệu. Điều này sẽ xác định xem liệu máy trộn có cần dùng lực chia cắt của cánh trộn hay không. Hoặc có phải dùng thêm một phương pháp khác như nghiền, rây nhằm phân tách các tiểu phân sau trộn. Một số loại máy trộn còn tồn tại những điểm chết, ở đó vật liệu không chuyển động hoặc chuyển động rất ít. Vị trí của những điểm chết này khác nhau ở các loại máy trộn, phụ thuộc nhiều vào phần trăm thể tích khối bột trộn trong máy, tốc độ máy trộn và lực kết dính giữa các tiểu phân.
– Một khi đã không chế được các yếu tố liên quan đến vật liệu, tiêu chí tiếp theo để lựa chọn máy trộn là các yếu tố liên quan đến quá trình. Máy trộn phải phù hợp với các điều kiện sản xuất sẵn có, phù hợp trộn cho nhiều loại sản phẩm và hoạt động tốt ở nhiều loại cỡ lô khác nhau. Nhiều loại máy trộn còn có thể kết hợp thêm chức năng khác như sấy, tạo hạt nhằm hạn chế tối đa quá trình vận chuyên vật liệu giữa các máy gây bay bụi và phân lớp vật liệu.
– Một yêu tố khác cũng cần xem xét khi lựa chọn máy trộn là hiệu quả sản xuất. Hiệu quả sản xuất liên quan đến tổng thòi gian để thực hiện một lô mẻ trộn, gồm thời gian để nạp nguyên liệu, thòi gian trộn, thời gian lấy mẫu, tháo nguyên liệu và vệ sinh máy. Các loại máy trộn có cánh khuấy bên trong thường khó và mất thời gian vệ sinh hơn các loại máy trộn chỉ có thùng chứa chuyển động.
Một số yêu cầu về thiết bị trộn
– Quá trình ma sát giữa các tiểu phân có thể sinh ra tĩnh điện, gây giảm hiệu suất trộn đối lưu và dính tiểu phân lên thành máy. Để tránh điều này, máy trộn nên được nối đất để triệt tiêu tĩnh điện và quá trình nên được tiến hành ở điều kiện ẩm lớn hơn 40%.
– Khối bột cần trộn không chiếm quá 75 % thể tích thiết bị.
– Các tiểu phân có thể chuyển dịch được theo cả ba chiều.
– Lực chia cắt thích hợp để có thể tránh sự kết tập các tiểu phân, nhưng mặt khác phải không được có các lực ly tâm để làm phân tách các tiểu phân do sự khác nhau về khối lượng.
– Các lực trộn không được gây ra sự gẫy vỡ các tiểu phân vì vậy tránh được sự phân tán không đều, do sự khác nhau về kích thước tiểu phân.
– Quá trình trộn nên được dừng đột ngột, giảm từ từ các lực trong một hướng có thể gây ra sự phân lập.
2.6.1. Thiết bị trộn kiểu nhào lộn
Thiết bị cấu tạo gồm một thùng trộn có khả năng quay xung quanh một trục cố định, bên trong thùng trộn chứa vật liệu trộn. Chuyển động nhào lộn của vật liệu trộn nhờ hoạt động quay của thùng trộn kết hợp với hình dạng thùng và đôi khi là các vách ngăn có mặt bên trong thùng. Với cách chuyển động này, cơ chế trộn chủ yếu của thiết bị là trộn khuếch tán, ngoài ra cũng có một phần trộn đôi lưu và biến dạng (chia cắt) ở mức thấp. Các thiết bị loại trộn nhào lộn được nắp kín khi vận hành và có thể vệ sinh dễ dàng do cấu tạo phía trong đơn giản. Một số loại thiết bị trộn được minh họa trong hình 2.2.
Hiệu quả của thiết bị trộn nhào lộn phụ thuộc rất nhiều vào tốc độ quay của máy. Tốc độ quá chậm sẽ khiến khối bột chuyển động không tốt, không tạo được sự nhào lộn và lực chia cắt như mong muốn. Ngược lại, tốc độ nhanh quá sẽ khiến bột bị ép dính lên thành máy do lực ly tâm, từ đó giảm hiệu quả của quá trình trộn. Tốc độ tốt nhất phụ thuộc vào hình dạng và kích thước của thùng chứa, cũng như bản chất khối bột. Nhìn chung, tốc độ này vào khoảng 30 đến 100 vòng/phút.
Máy trộn nhào lộn phù hợp với khối lượng từ 50g ở quy mô phòng thí nghiệm đến khoảng 100 kg trong công nghiệp. Trong đó, khối bột chiếm khoảng từ 1/2 đến 2/3 thể tích máy.
Máy trộn kiểu nhào lộn phù hợp với khối bột có độ chảy tốt, do lực chia cắt không đủ để phá vỡ các tiểu phân bị kết tập. Cũng cần chú ý nếu khối bột có sự phân bố kích thước rộng do dễ có khả năng phân lớp. Loại máy trộn này thường dùng để trộn hạt khô.
2.6.2. Các thiết bị trộn không tạo chuyển động nhào lộn
Các thiết bị trộn loại này không tạo sự nhào lộn của hỗn hợp nguyên liệu trong quá trình trộn; vì vậy, không tạo ra sự phân lập liên tục như các thiết bị loại trên. Loại thiết bị trộn này tạo lực chia cắt lớn, thích hợp để trộn các hỗn hợp có khả năng kết dính lớn. Chúng thường được sử dụng để nhào trộn các khối hạt ẩm trong quá trình tạo hạt. Các thiết bị không tạo chuyển động nhào lộn gồm một số loại chính như: thiết bị trộn cao tốc, thiết bị trộn có cánh trộn dạng dải xoắn, thiết bị trộn hành tinh.
2.6.2.1. Máy nhào trộn cao tốc
Máy cấu tạo gồm một thùng chứa kín bằng thép (hình 2.3). Bên trong thùng chứa có hệ thông cánh đẩy, nằm phía đáy thùng, chuyển động với tốc độ cao theo mặt phẳng nằm ngang, và hệ thống dao cắt, nằm phía trên thành, chuyển động quay tròn. Cánh đẩy được thiết kế để chuyển động với tốc độ 150-300 vòng/phút trong khi đó dao cắt có thể quay tối 1500-3000 vòng/phút.
Cơ chế trộn của máy là sự kết hợp của lực chia cắt và trộn khuếch tán. Khi cánh đẩy quay, khối bột chịu tác động của lực li tâm, bị đẩy vào thành máy, chuyển động lên cao rồi lại rơi vào phía tâm. Hệ thống dao cắt có nhiệm vụ đánh tơi khối bột chuyển động xung quanh thành máy.
Máy có thể hoạt động theo cơ chế liên tục nhờ việc đưa nguyên liệu vào phần trên máy và lấy nguyên liệu phía dưới. Với loại máy trộn này, cần chú ý trong quá trình trộn nhiệt độ khối bột có thể tăng nhẹ. Lưu ý khi trộn các loại vật liệu dễ bị vỡ. Máy thường không dùng để trộn tá dược trơn.
2.6.2.2. Máy nhào trộn dạng dải xoắn
Cấu tạo gồm hai dải xoắn gắn chung vào một trục chuyển động ngang trong máng hình bán nguyệt.
Máy hoạt động theo cơ chế trộn đối lưu, có thể trộn được cả những nguyên liệu trơn chảy kém và ít gây ra hiện tượng phân lớp so vối kiểu trộn nhào lộn. Nhược điểm là máy có những điểm chết mà trục xoắn không tác động tới khối bột.
2.6.2.3. Máy nhào trộn kiểu hành tinh
Dùng nhào trộn cả dạng bột và dạng bán rắn. Thùng trộn được đặt phía dưới và có thể tách ròi để có thể dễ dàng nạp và tháo nguyên liệu.
Cánh khuấy tham gia đồng thời hai chuyển động: chuyển động tròn theo chu vi của thùng trộn và chuyển động xung quanh trục của chính nó. Điều này giống như chuyển động của hành tinh xung quanh mặt trời nên máy có tên gọi là máy nhào trộn kiểu hành tinh.
Giống như loại máy trộn dạng dải xoắn, máy nhào trộn kiểu hành tinh cũng có những điểm chết mà vật liệu trộn không chuyển động hoặc chuyển động rất ít. Do vậy với những máy trộn loại này, quá trình lấy mẫu kiểm tra và thẩm định phải đặc biệt ch ý vừa để đảm bảo độ đồng nhất của khối bột, vừa nhằm tìm ra những vùng có nguy cơ chưa đều.
2.6.2
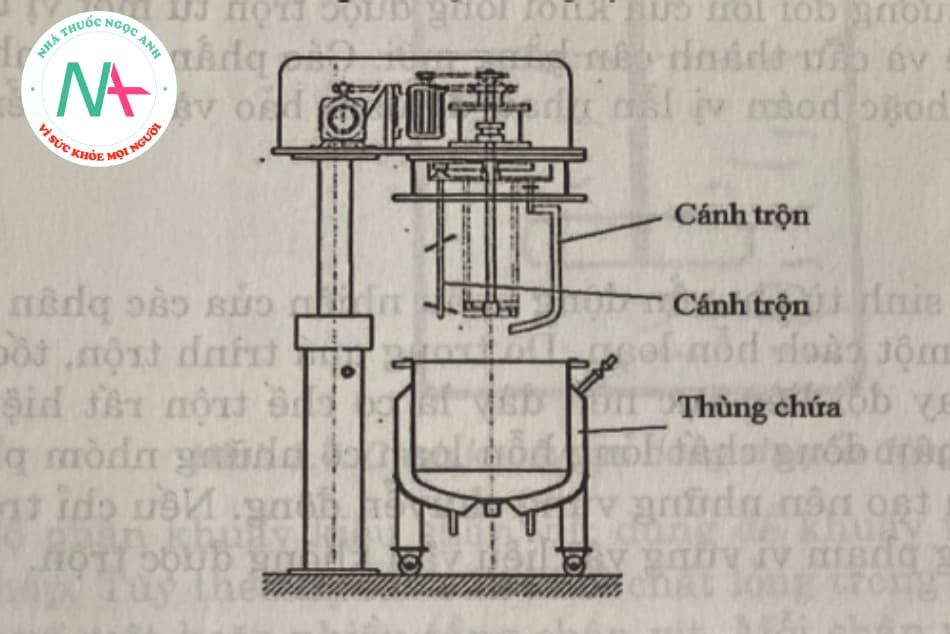
2.6.2.4. Máy nhào trộn kiểu tầng sôi
Loại máy trộn này sử dụng luồng khí có vận tốc lớn, thổi vào khối bột cần trộn nhằm làm “giãn nở” khối bột và chuyển động các tiểu phân trong đó. Máy trộn kiểu tầng sôi chỉ được sử dụng khi theo sau quá trình trộn là các quá trình khác (như tạo hạt ướt, sấy). Nhược điểm của máy trộn loại này là luôn tạo một lớp mỏng vật liệu mịn ở trên bề mặt khôi bột.
3. Trộn chất lỏng và hỗn dịch
3.1. Cơ chế trộn
Các cơ chế trộn chất lỏng về cơ bản thuộc vào 4 loại: vận chuyển khối, dòng chảy hỗn loạn, dòng chảy lớp và khuếch tán phân tử.
3.1.1. Vận chuyển khối
Tương tự như cơ chế trộn đối lưu của bột, vận chuyển khối là sự dịch chuyển của một phần tương đối lớn của khối lỏng được trộn từ một vị trí đến một vị trí mới trong hệ và cấu thành cân bằng mối. Các phần khác nhau đó phải được tái sắp xếp hoặc hoán vị lẫn nhau để đảm bảo vận chuyển khối đạt hiệu suất cao.
3.1.2. Trộn hỗn loạn
Trộn hỗn loạn phát sinh từ chuyển động ngẫu nhiên của các phân tử khi bị buộc phải di chuyển một cách hỗn loạn. Do trong quá trình trộn, tốc độ và hướng chuyển động thay đổi liên tục nên đây là cơ chế trộn rất hiệu quả. Tuy nhiên, trong bản thân dòng chất lỏng hỗn loạn có những nhóm phân tử chuyển động cùng nhau tạo nên những vùng chuyển động. Nếu chỉ trộn hỗn loạn đơn thuần thì trong phạm vi vùng vật liệu vẫn không được trộn.
3.1.3. Trộn lớp
Trộn lớp thường xảy ra khi trộn các dịch lỏng có độ nhớt cao hoặc ở những vùng chất lỏng chuyển động chậm rãi (khi cánh khuấy quay chậm hoặc những vùng nằm sát với các bề mặt tĩnh của thùng chứa). Quá trình trộn thường xảy ra trên bề mặt giữa hai lớp.
3.1.4. Khuếch tán phân tử
Đây là hình thức trộn ở mức độ phân tử, là kết quả của sự khuếch tán do chuyển động nhiệt. Quá trình tuân theo định luật thứ nhất của Fick về khuếch tán:
dm/dt=-DA(dc/dx)
Vận tốc chuyển khôi (dm/dt) qua một bề mặt có diện tích A (đặt vuông góc với chiều khuếch tán) tỷ lệ với A, với chênh lệch nồng độ theo khoảng cách (dc/dx) và hệ số khuếch tán D. Hệ số khuếch tán phụ thuộc vào độ nhớt dịch lỏng và kích thước của phân tử khuếch tán.
3.2 Các loại máy trộn
3.2.1. Máy trộn có cánh khuấy
Máy trộn có cấu tạo gồm hai bộ phận chính: thùng chứa là nơi quá trình trộn diễn ra và bộ phận khuấy để tạo chuyển động cho dòng chất lỏng. Thùng chứa có thể có các vách ngăn đổi hướng làm tăng sự chuyển động của dịch, đồng thời hạn chế sự tạo thành dòng xoáy ở giữa chất lỏng. Bộ phận khuấy được chia thành nhiều loại, mỗi loại dùng để trộn hôn hợp lỏng có độ nhớt khác nhau.
– Bộ phận khuấy kiểu chân vịt: dùng để khuấy trộn các chất lỏng có độ nhớt thấp. Tùy theo độ cao của khối chất lỏng trong thùng chứa, người ta có thể bố trí một hoặc nhiều tầng chân vịt. Mỗi chân vịt thường gồm ba cánh được bố trí vát nghiêng so với mặt phẳng nằm ngang một góc α.
Dạng cánh nghiêng như vậy đảm bảo tạo ra dòng chảy hướng trục rất lớn, bao gồm cả chuyển động đi vào và đi ra khỏi cánh khuấy, qua đó rút ngắn được thời gian khuấy trộn. Tỷ lệ giữa đường kính của cánh khuấy kiểu chân vịt với đường kính thùng trộn thường trong khoảng 1:10 tới 1:20, tốc độ có thể đạt tới 8000 vòng/phút.
– Bộ phận khuấy kiểu tuabin: dùng khuấy trộn hỗn hợp chất lỏng có độ nhớt cao. Cấu tạo tua bin gồm nhiều cánh đặt trên một đĩa tròn quay xung quanh trục thẳng đứng. Cánh tua bin có thể thẳng, nghiêng hoặc cong.
Loại cánh thẳng có thể tạo dòng chảy tiếp tuyến và hướng tâm trong đó chất lỏng được hút vào tâm và đẩy ra theo chu vi cánh. Loại cánh nghiêng giúp tạo dòng hướng tâm và hướng trục giúp khuấy trộn tốt những vật liệu rắn trong chất lỏng. Còn loại cánh cong tạo dòng tiếp tuyến và hướng tâm.
Bao xung quanh các cánh khuấy có thể bố trí vòng đai có đục lỗ với kích thước thích hợp. Chất lỏng khi đó sẽ được đẩy qua các lỗ nhỏ của vòng đai tạo lực chia cắt lớn. Khi khuấy trộn chất lỏng không đồng tan, nếu kích thước lỗ đủ nhỏ và tốc độ quay đủ lớn, lực chia cắt sẽ giúp hình thành các giọt phân tán bền vững. Máy trộn kiểu tuabin do đó thường được ứng dụng bào chế nhũ tương hay kem.
– Bộ phận khuấy kiểu tấm: có thể khuấy trộn hỗn hợp chất lỏng có độ nhớt cao. Các tấm khuấy thường có diện tích bề mặt tương đối lớn so với thùng chứa nên có khả năng quét rất rộng. Tốc độ của cánh khuấy khá thấp và khi quay tạo ra dòng chảy tiếp tuyến.
3.2.2. Máy trộn dùng khí nén
Khí nén (thường là không khí hoặc nitơ) được thổi qua một lỗ nhỏ từ đáy thùng chứa vào dung dịch. Bọt khí sinh ra nổi lên bề mặt kéo theo dòng chất lỏng chuyển động và đảo đều hỗn hợp. Quá trình có thể được hỗ trợ nhờ một ông hút lớn đặt trong thùng trộn nhằm khu trú chuyển động của lượng bọt sinh ra. Với thiết bị khuấy trộn dùng khí nén, chất lỏng khuấy trộn phải có độ nhớt thấp, không tạo lớp bọt trắng phía trên bề mặt, không tương tác với khí sử dụng và ít bay hơi.
3.2.3. Máy trộn dùng bơm tuần hoàn chất lỏng
Các hỗn hợp chất lỏng có độ nhớt thấp còn có thể được khuấy trộn bằng phương pháp bơm tuần hoàn chất lỏng. Có nhiều cơ chế bơm khác nhau để tạo sự luân chuyển tuần hoàn chất lỏng trong thùng chứa, một trong số đó là cách sử dụng phòng hút.
Hỗn hợp trộn được bơm qua vòi phun thứ nhất vào phòng hút. Do lực bơm rất mạnh, tốc độ bơm có thể đạt 10-20m/s, một phần chất lỏng bên ngoài bị hút vào phòng tạo nên sự xáo trộn mạnh giữa hai dòng chất lỏng trong phòng. Hỗn hợp sau khi trộn được thoát ra ngoài qua vòi phun thứ hai, tiếp tục quá trình trộn với phần hỗn hợp còn lại trong thùng chứa, với lực trộn yếu hơn.
CÂU HỎI LƯỢNG GIÁ
- Cách đánh giá quá trình trộn?
- Các cơ chế của quá trình trộn rắn, lỏng?
- Các yếu tố ảnh hưởng đến quá trình trộn rắn, lỏng?
- Các kỹ thuật trộn chất rắn?
- Cấu tạo, nguyên tắc hoạt động, ưu nhược điểm và ứng dụng trong công nghiệp dược phẩm của các thiết bị trộn?